Design Build Fly (DBF)
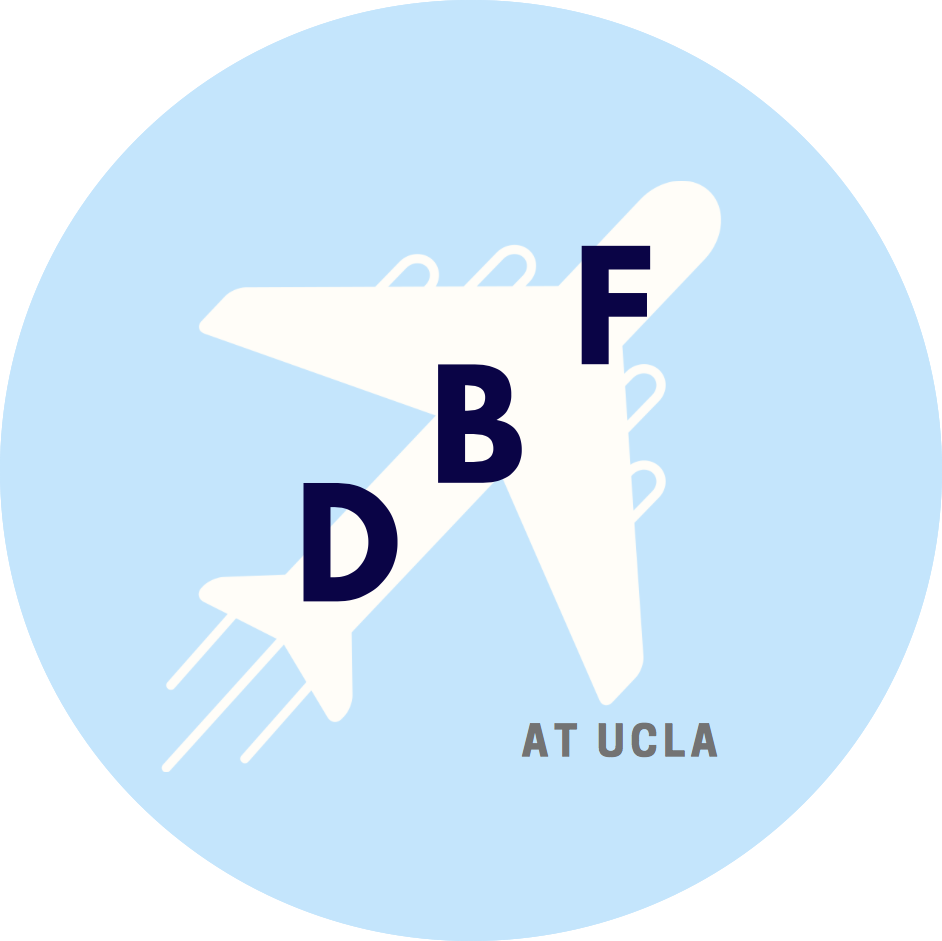
Design Build Fly (DBF) at UCLA competes in the annual international AIAA DBF Competition with 100+ other collegiate teams. Each year, the teams are given new specific mission requirements to complete, including flight speeds, payload carrying, sensor deploying, and more. Our team of 30 interdisciplinary engineers come up with the solution that best satisfy the mission requirements while optimizing flight performances.
2022 - 2023: Project Manager
As the Project Manager of our team, I am grateful for this opportunity to lead this team of talented engineers. I'm looking forward to another year of designing, building, and flying. Our goal is to reach top 10% in overall scores, which would set a historic record for us.
2021 - 2022: Vice Project Manager
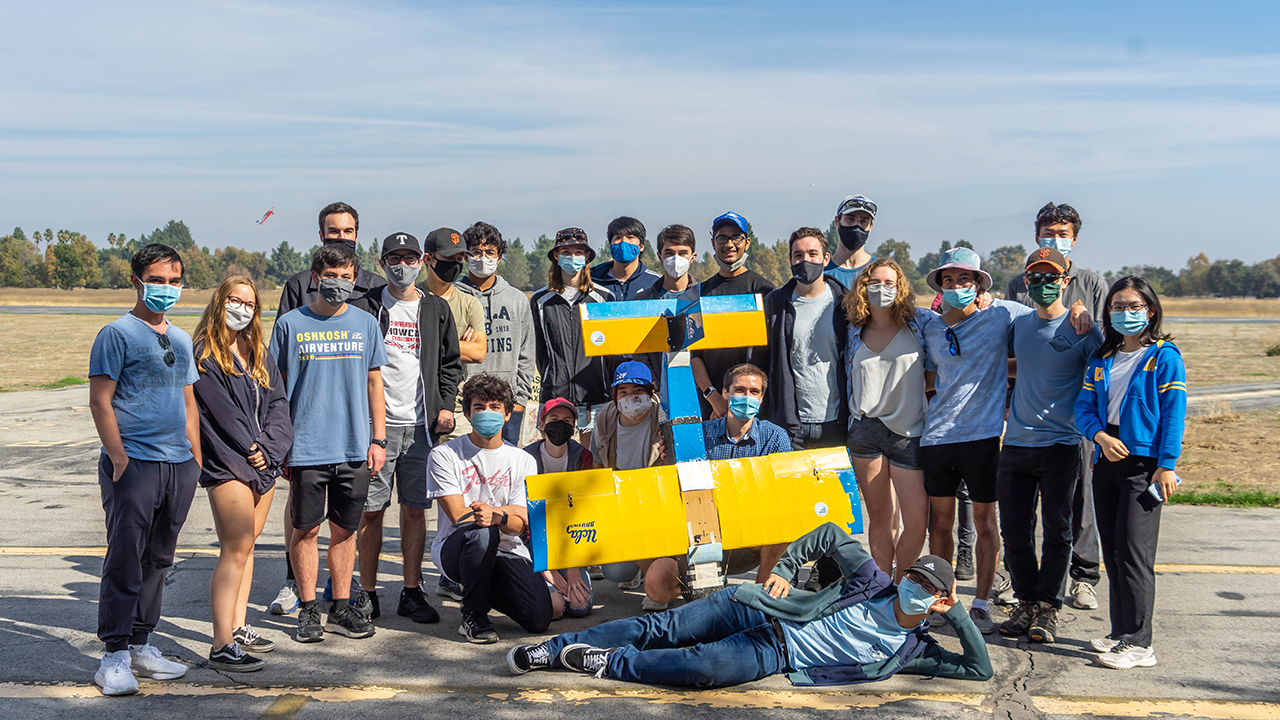
Team Fly Day
Competition Team in Kansas
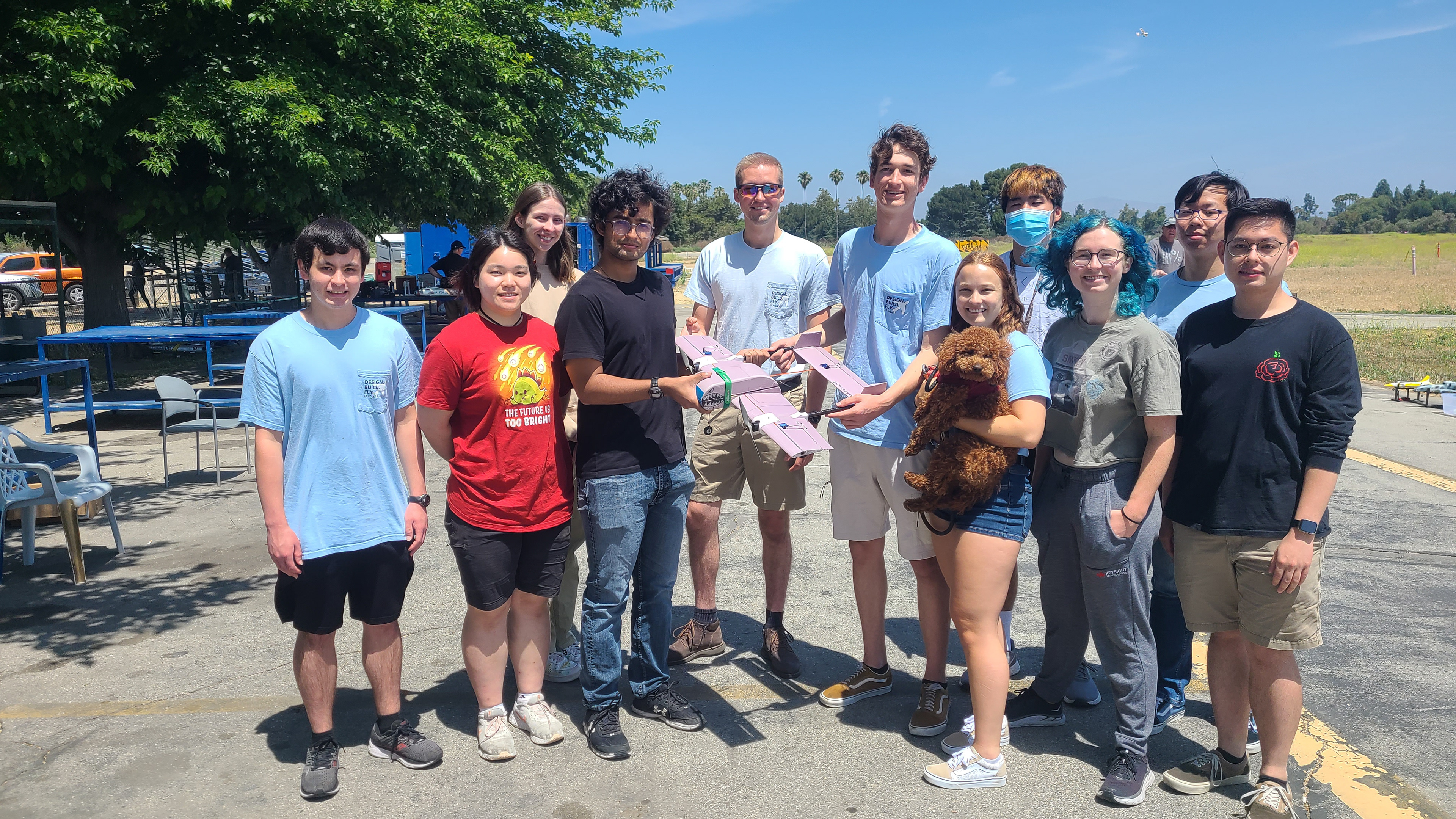
R&D Team Fly Day
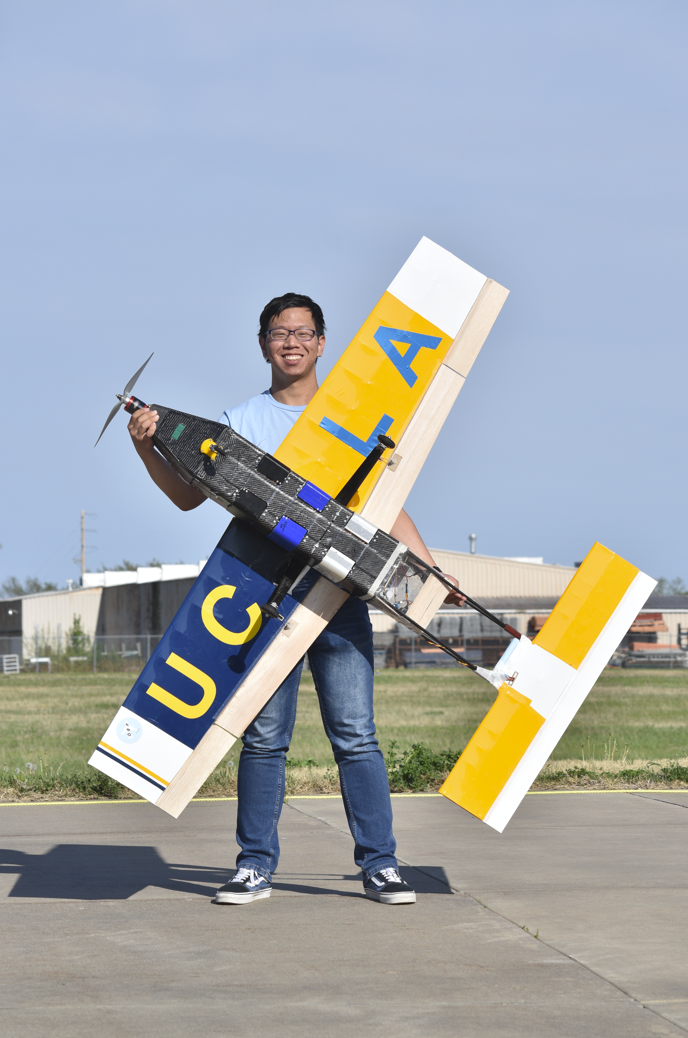
Lazarus in Flight at Competition
Lazarus in Flight at Competition
Objectives
- Restrictions: linear dimension less than 8', total takeoff weight less than 55lb, electrically powered and propeller driven, 100 Wh battery, takeoff field of 25'.
- Flight Mission: complete 3 laps in 5 minutes.
- Syringe Mission: carry "syringes" and complete 3 laps as fast as possible.
- Package Deployment Mission: carry as many "vaccine vial packages" (3.5" x 3" x 2.5"; 25g shock sensors) as possible, and land and deploy one package after each lap without triggering the sensors, in 10 minutes.
Skills
Mechanical Design: SolidWorks, design for manufacturing
Simulation: SolidWorks FlowSim, AVL
Prototyping: 3D (FDM) printing, prototype testing, data collection & analysis, failure testing
Programming: MATLAB
Electronics: Arduino, propulsion electronics
Manufacturing: laser cutter, drill press, carbon fiber wet layup process
Machine Tools: Dremel, sander, heat tools, adhesives, fasteners, hand tools
Management: Financial tracking, event planning, Gantt charts, team leadership
Key Tasks
My tasks and contributions span across administrative and technical tasks.
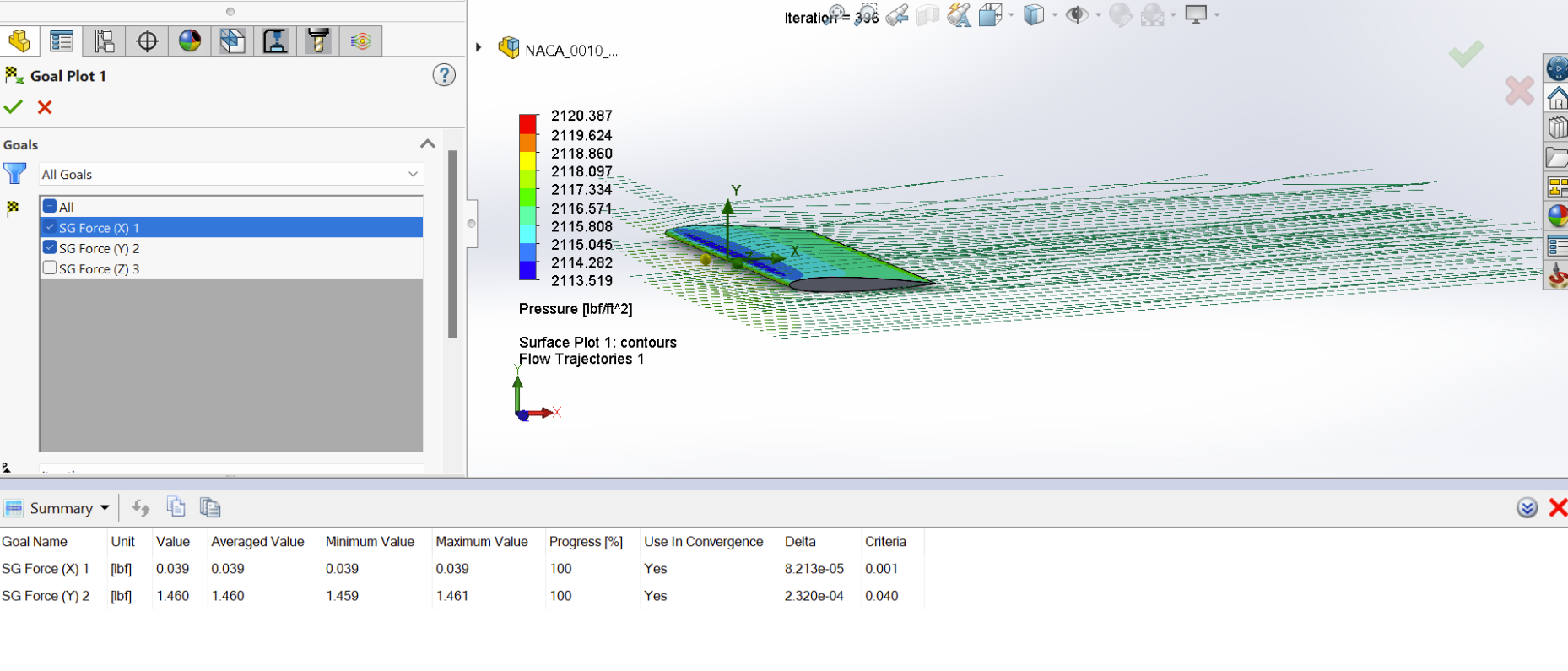
NACA 0010 at 4 deg AoA
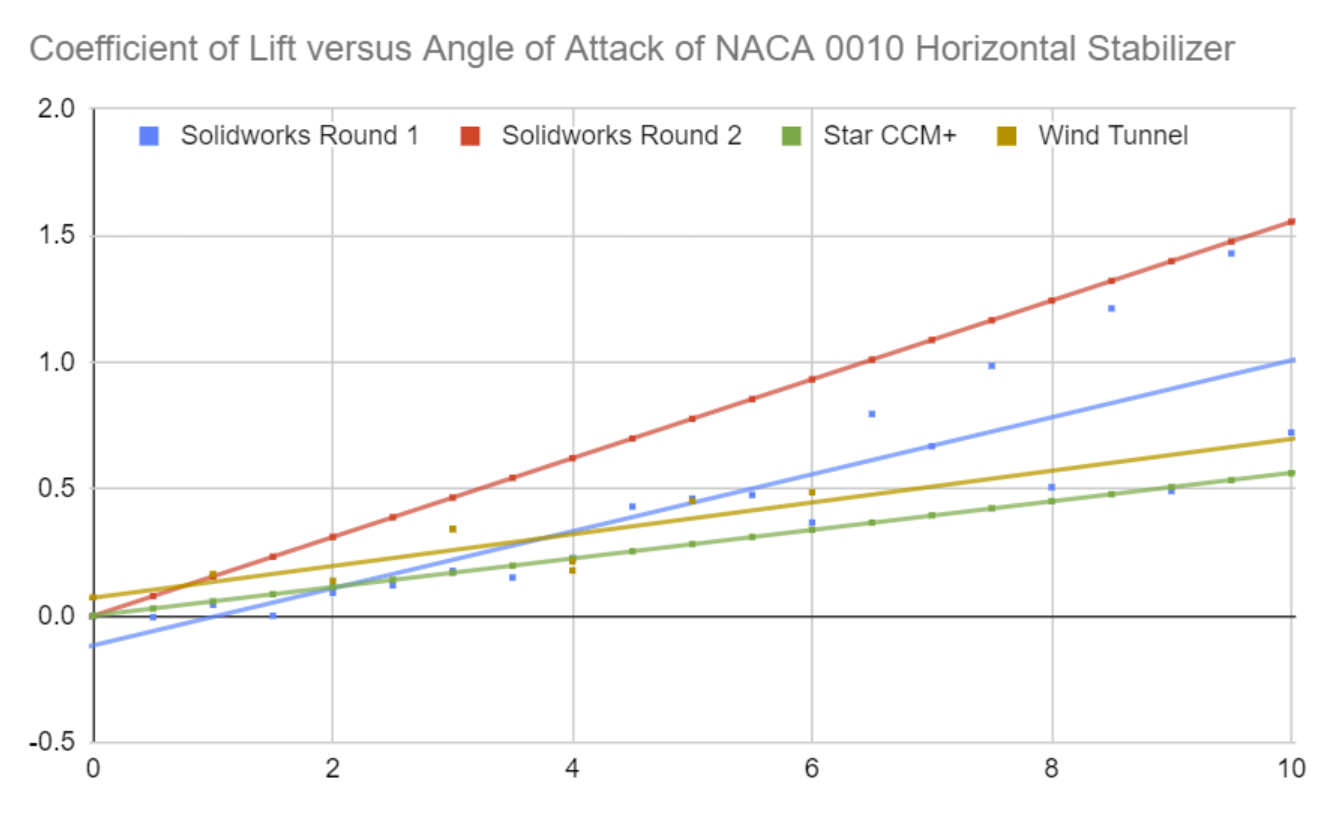
NACA 0010 Simulated and Experimental Data
Aerodynamics
- Conducted trade study of available airfoil data; picked Martin Hepperle (MH) 115 as the primary wing airfoil and NACA 0010 as the horizontal stabilizer airfoil
- Researched nose cone and tail cone geometries to minimize drag.
- Researched wingtips and flap configurations to minimize drag through different flight regimes.
- Used SolidWorks FlowSim to conduct Computational Fluid Dynamics (CFD) on the airfoil to verify lift and drag at various angles of attack.
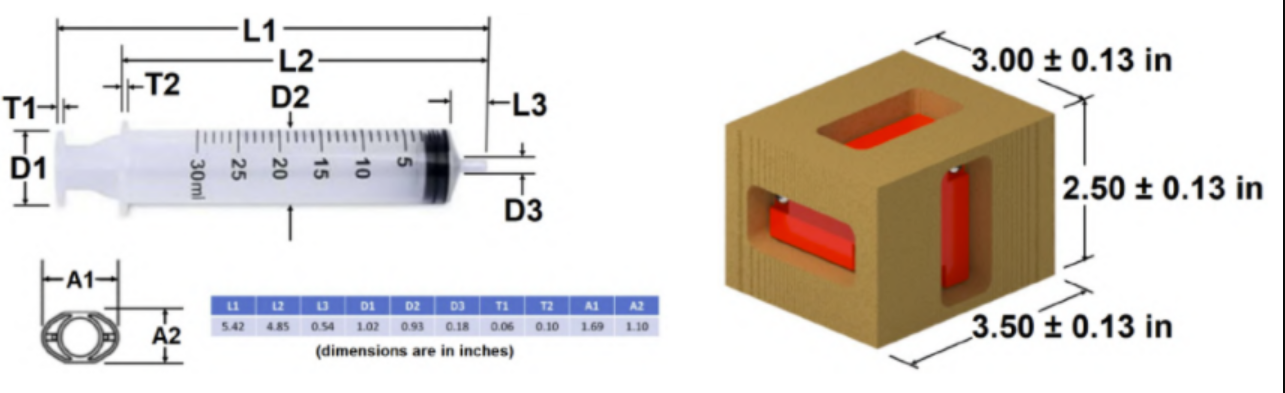
Mechanism Dimensions
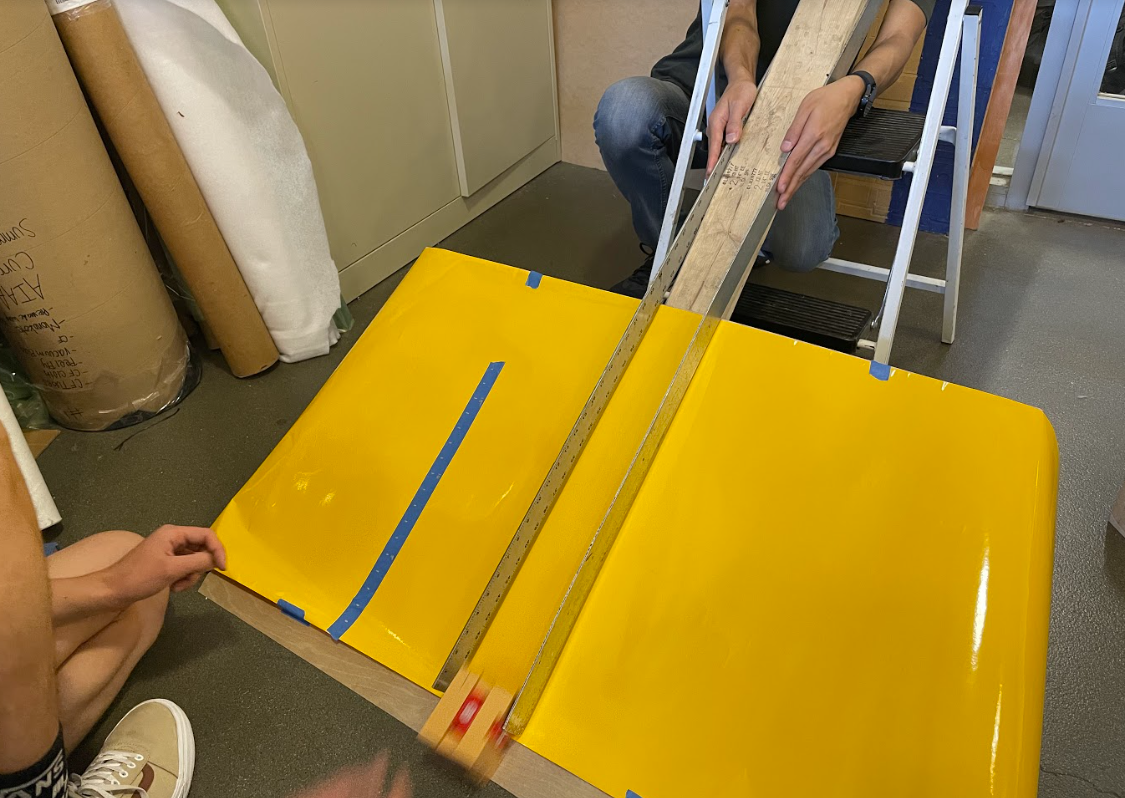
Initial Deployment Testing
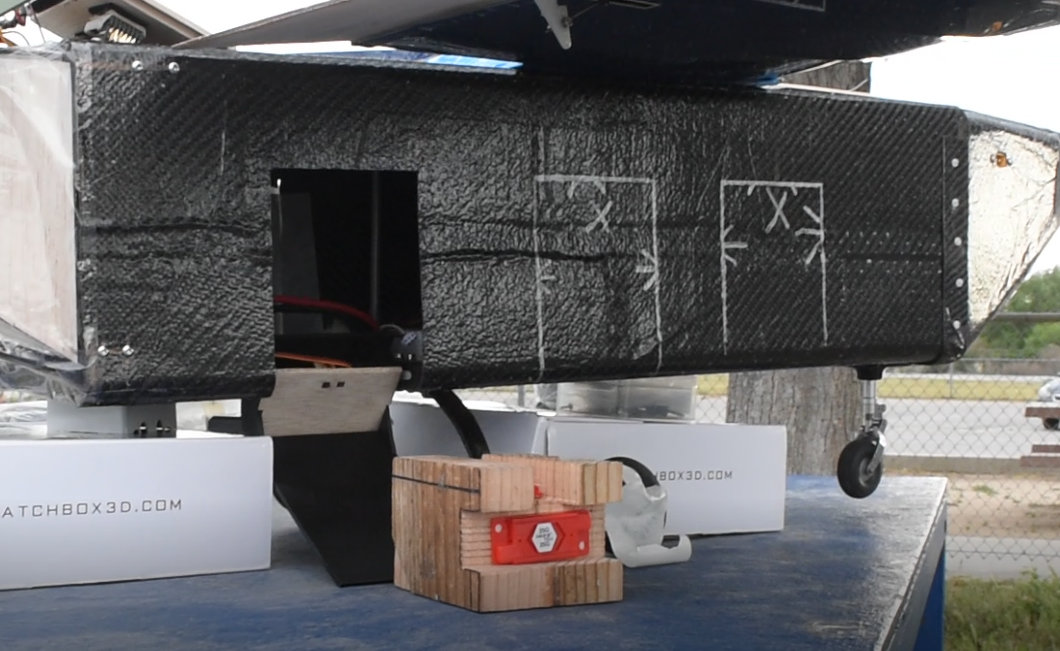
Final Deployment Mechanism
Mechanism
- Led initial experiments in testing maximum drop height without triggering the package shock sensors.
- Experimented with ramp surface and height, and used the data to inform deployment mechanism sizing.
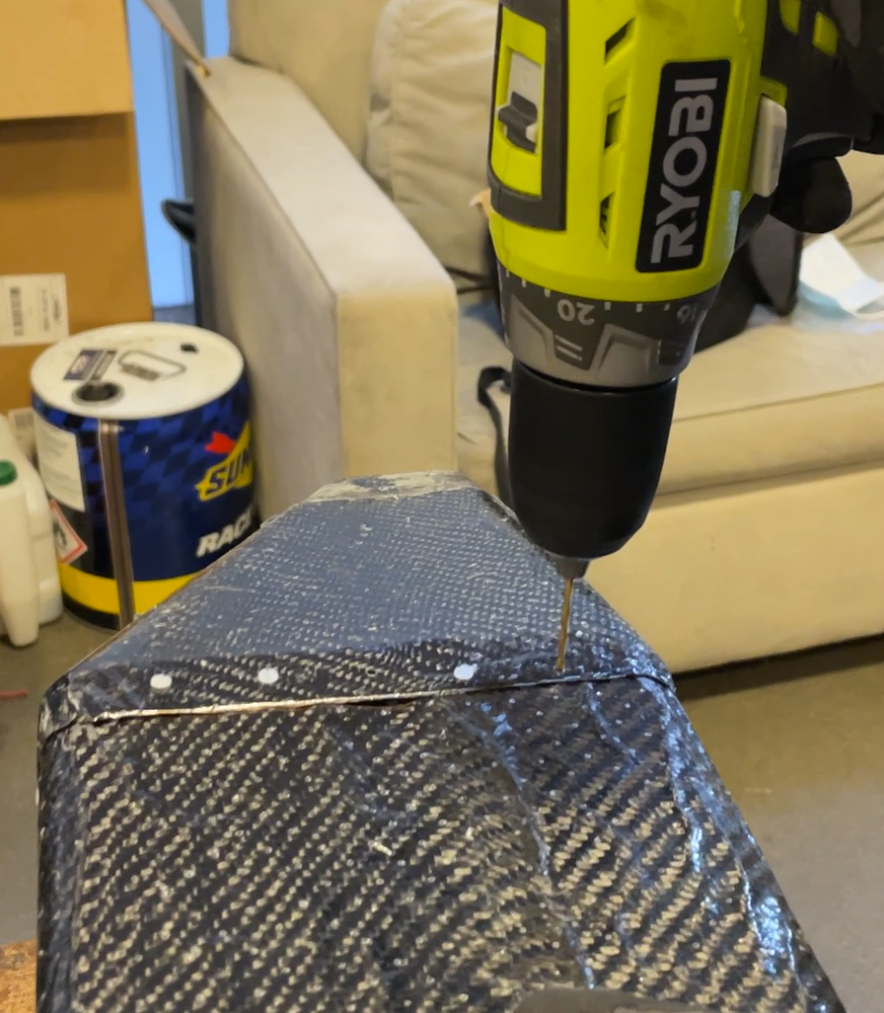
Drilling Bolt Holes in the Fuselage
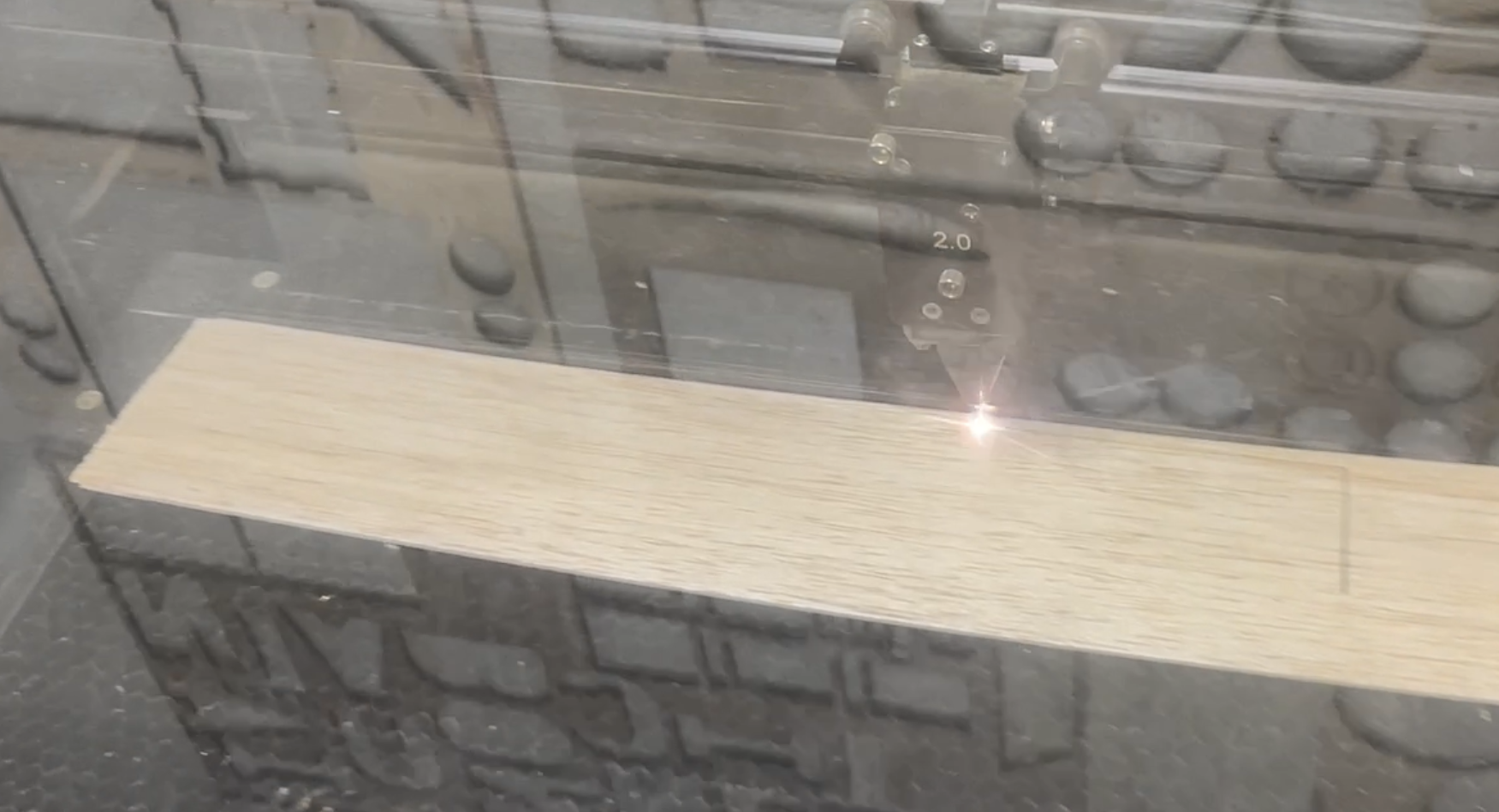
Laser Cutting Balsa Sheets
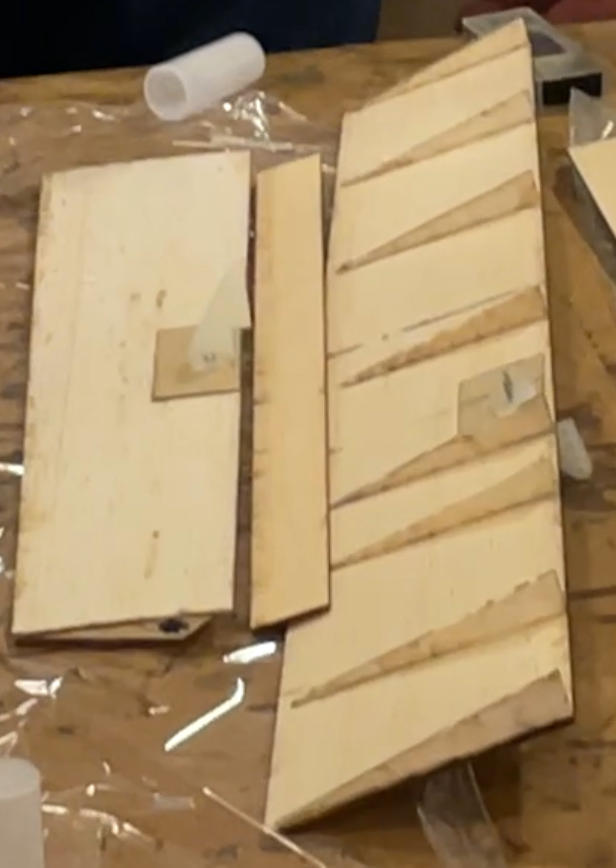
Gluing Control Surface Pieces
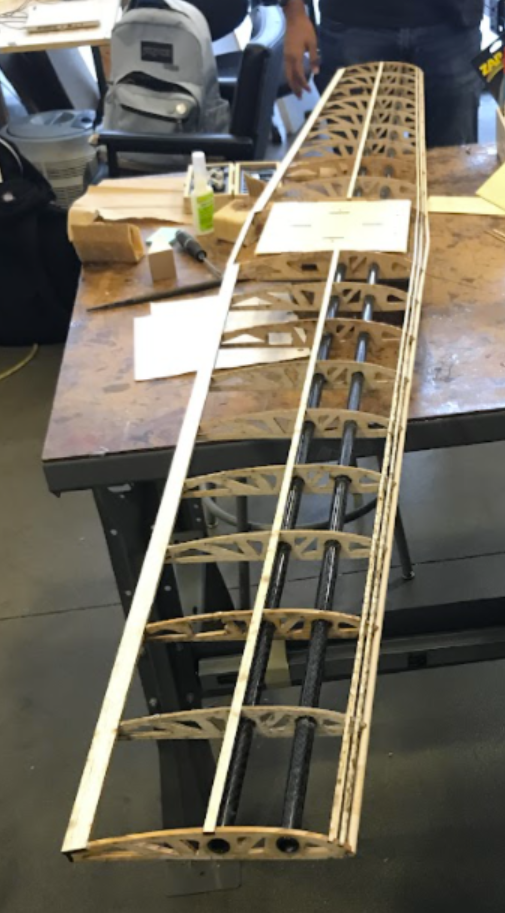
Wing Ribs
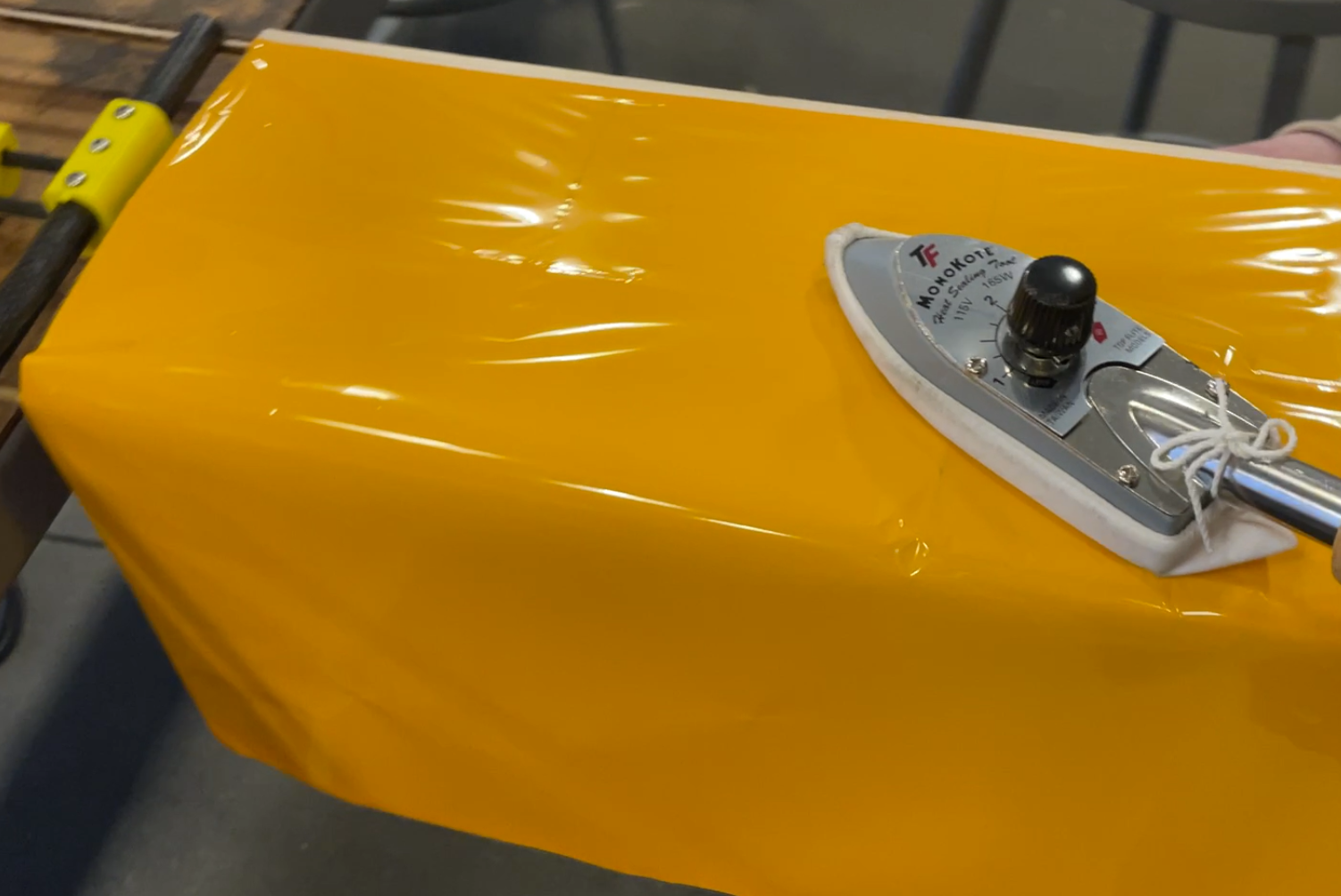
Applying MonoKote
Manufacturing
- Used handheld drills, drill presses, bandsaws, hand saws, and Dremel to create holes and openings for the motor mount, fuselage access hatches, electrical wiring, and general fastener uses.
- Utilized the carbon fiber wet layup process and 3D-printed molds to create the nose cone and the fuselage.
- Laser cut and assembled balsa and spruce ribs, alignment jigs, surface pieces, motor mount, wing box, control surface, etc.
- Put on heat-shrinking MonoKote wrap using heating irons and heating guns.
- Strategically applied metal and nylon bolts, nuts, velcro, cyanoacrylate (CA) glues, epoxies, and other fasteners and adhesives to securely mount and interface aircraft components.
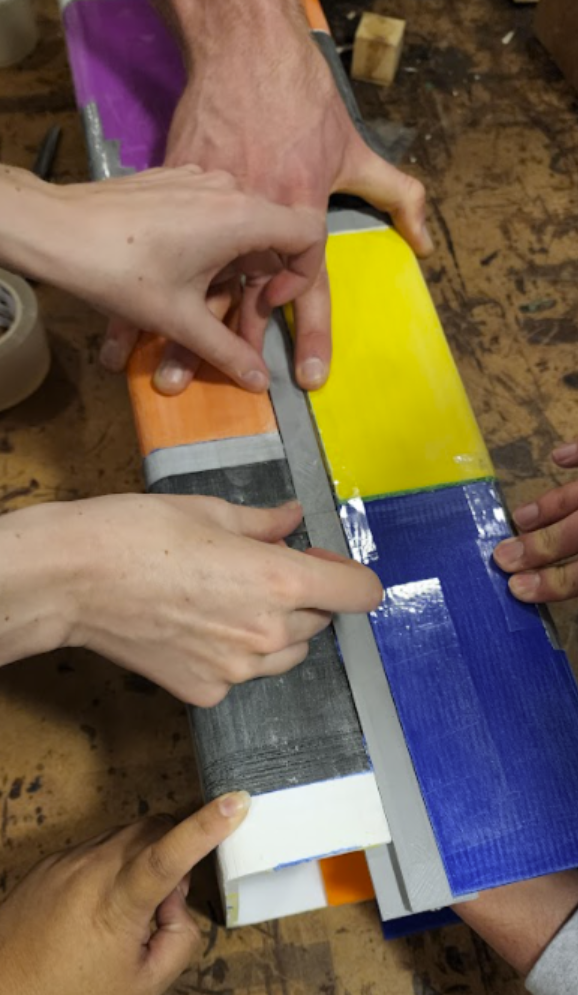
Preparing Molds
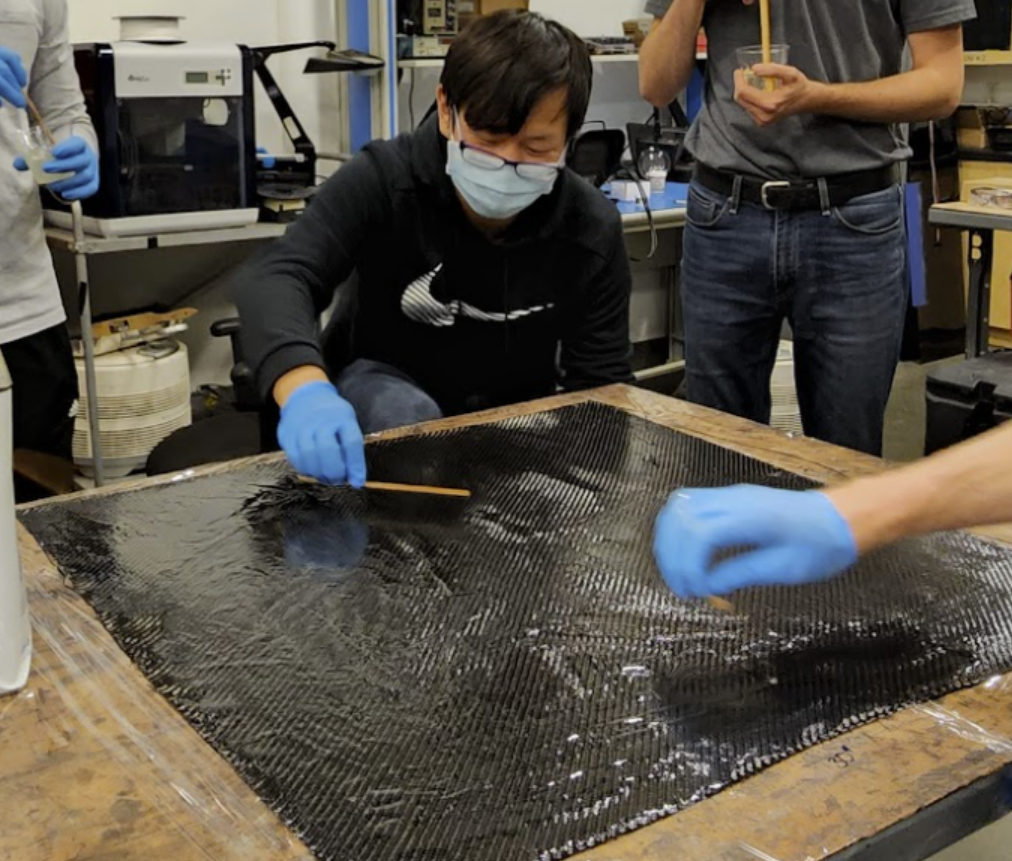
Carbon FIber Layup
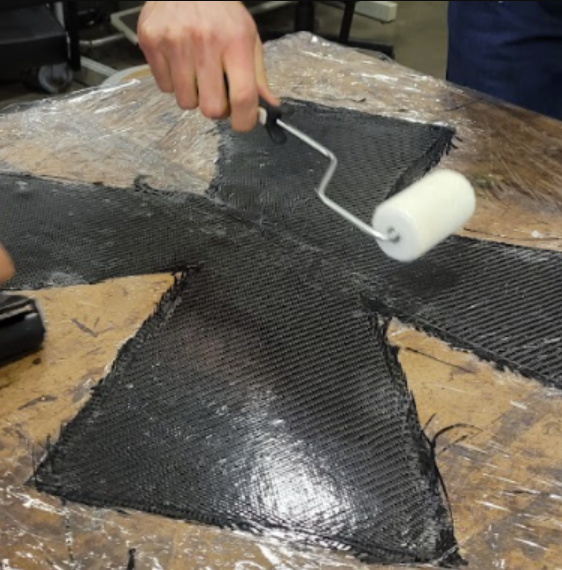
Carbon Fiber Layup
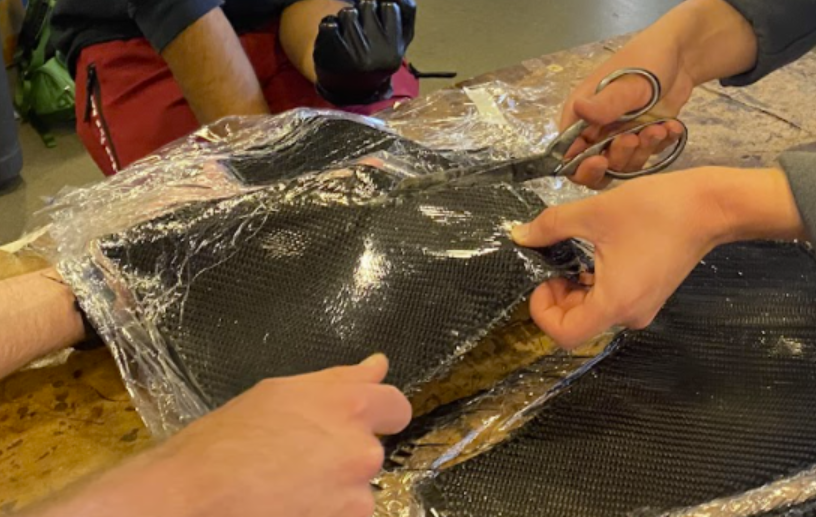
Carbon Fiber Layup
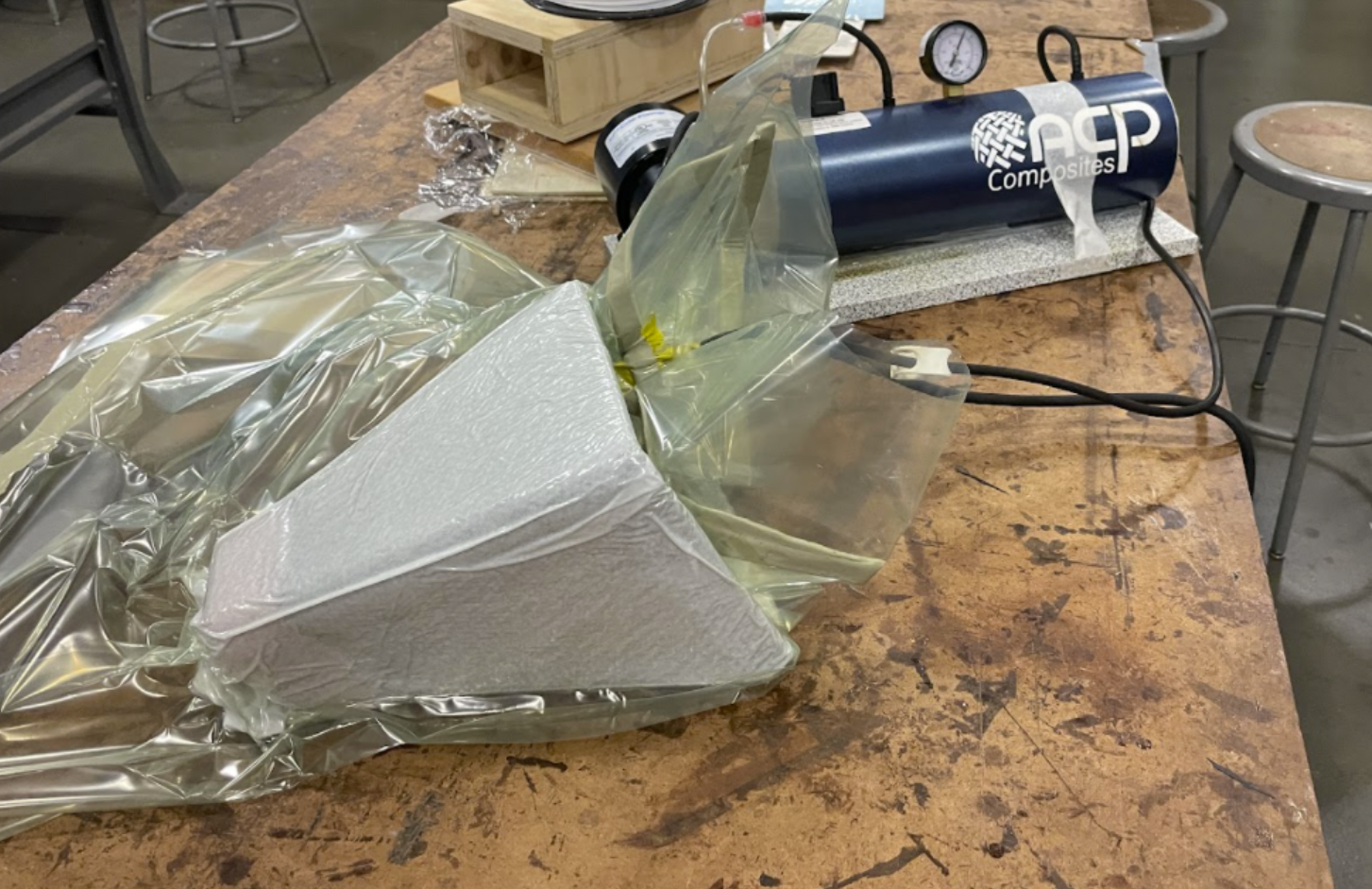
Nose Cone in Vacuum Bag
Administrative
- Assisted the leadership in designing, prototyping, and testing a well-functioning aircraft under a $8800 total budget for the annual international AIAA DBF competition.
- Acquired $2200 funding by presenting the organization in front of the Engineering Alumni Association.
- Certified component and assembly quality throughout the design and manufacturing process.
- Created and maintained a Discord server for club-wide technical and social communication.
- Coordinated COVID safety regulations to ensure adaptability and adherence to UCLA guidelines.
- Facilitated team growth and continuous improvement via anonymous feedback forms.
- Created graphics and visuals for the project proposal and budget proposal.
- Spearheaded the planning of logistics for the week-long trip to and from the Wichita, Kansas competition site, including itinerary, transportation, housing, food, and safety.
- Accelerated the 60-page design report writing process by hosting workdays, task organization, and purposeful delegation.
Outcomes
- Our final competition aircraft, Vax Express (later renamed Lazarus), has a high-mounted 6' wingspan with a 9.25" chord and a MH 115 airfoil. It is pulled by a single Cobra C-4130/12 motor and a 3-bladed 14x9 Master Airscrew (MAS) propeller and a 99Wh 6S LiPo battery.
- The aircraft has a takeoff weight of 12lb in the Flight Mission and 15lb fully loaded in the Package Deployment Mission, and has an airspeed of 80ft/s. It carries 60 syringes in the Syringe Mission and 6 packages in the Package Deployment Mission.
- During competition, under barrage from 50mph wind, Vax Express crashed into the runway. However, using existing resources, our team fixed the broken sections and installed a new propulsion system.
- Placed 6th / 97 (6.2%) in the design report and 16th / 64 (25%) overall in the annual AIAA DBF competition, a historic high for our team since 2008.
- Throughout this year, I experienced a full product design cycle through 2 iterative prototypes and a successful final product. I worked not only on all parts of the technical design and testing, but also led the administration of the team in budget, time, and safety management.
2020 - 2021: Aerodynamics, CAD, & Manufacturing Engineer
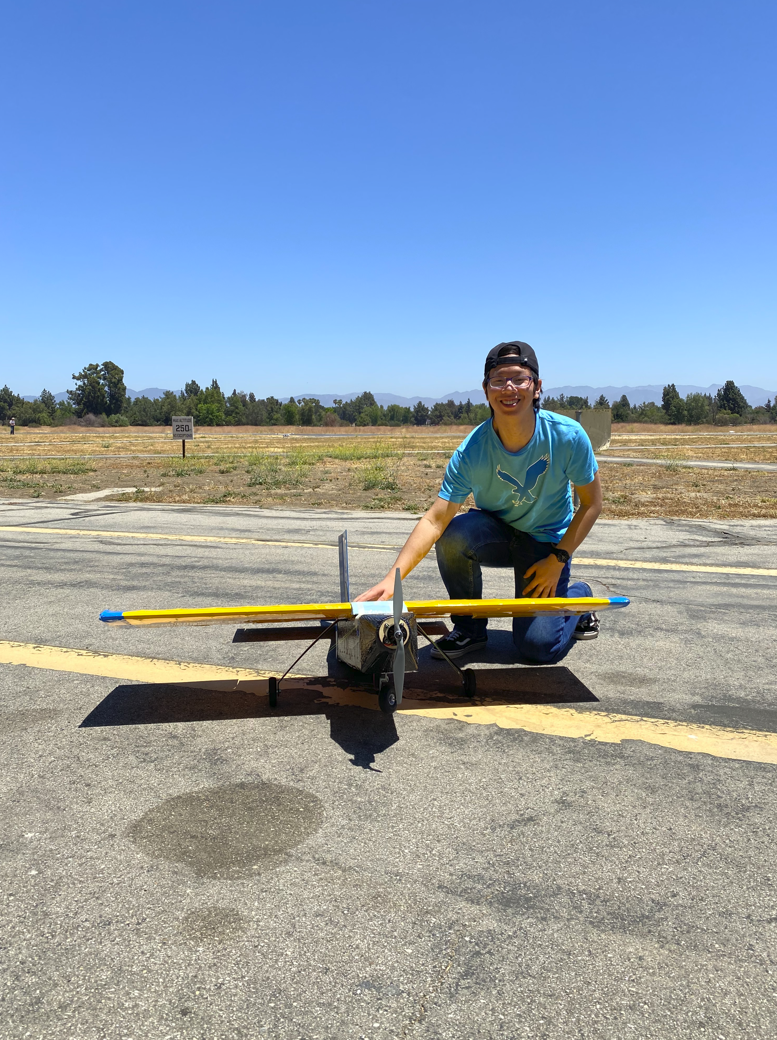
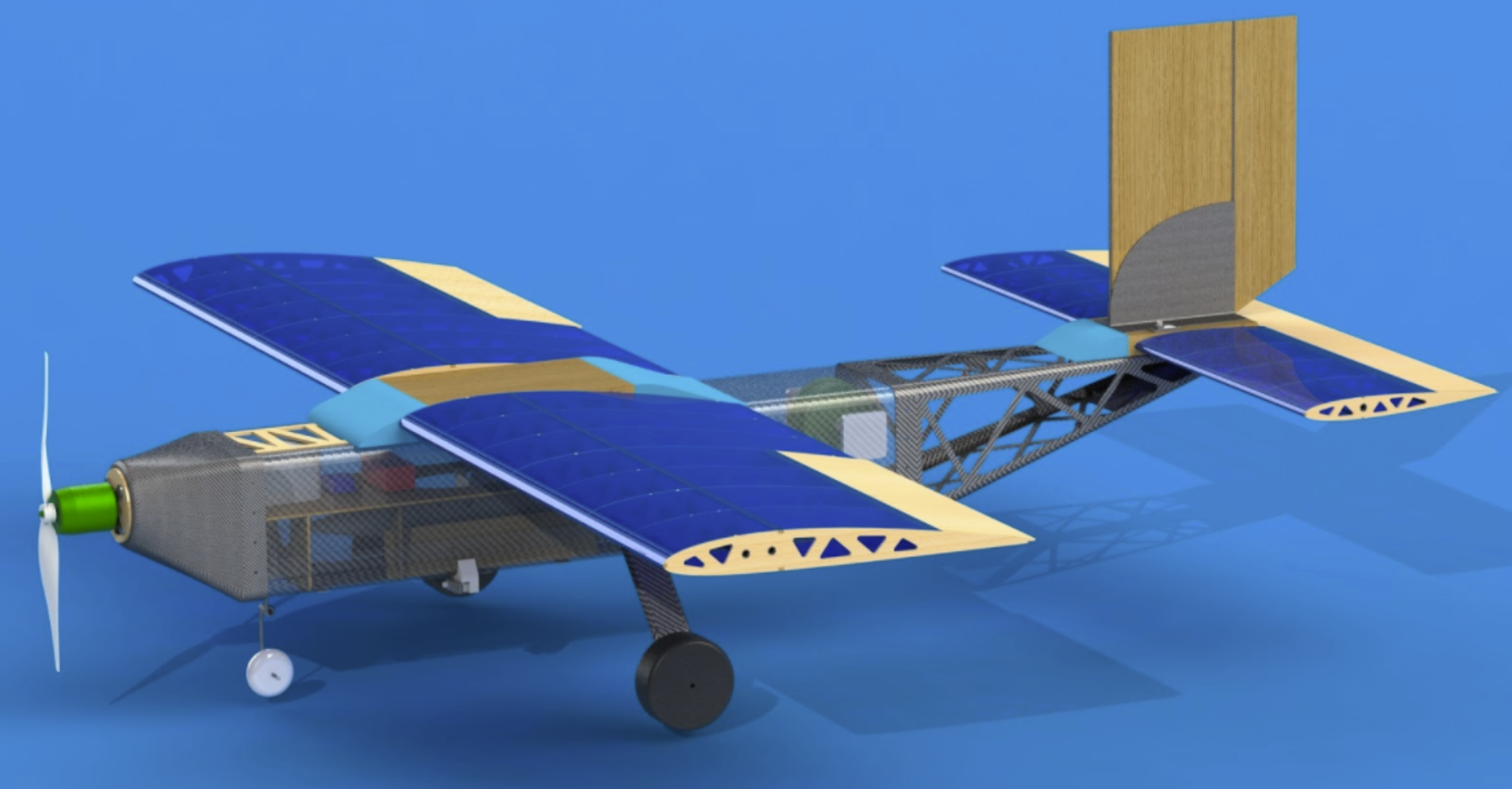
Patchwork Rendered CAD
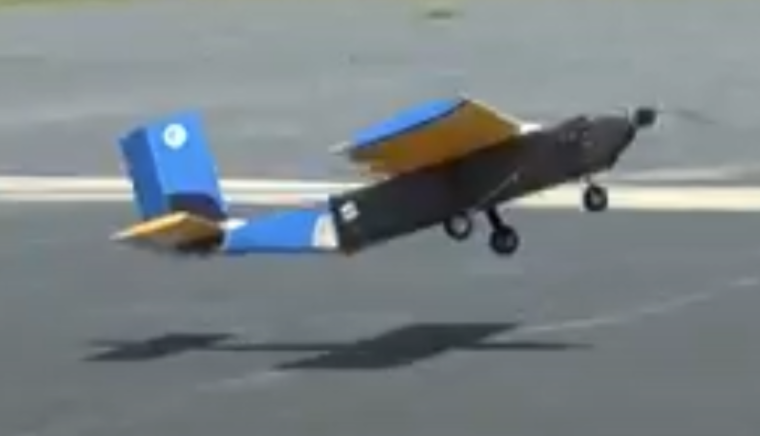
Patchwork Taking Off

Patchwork in Flight
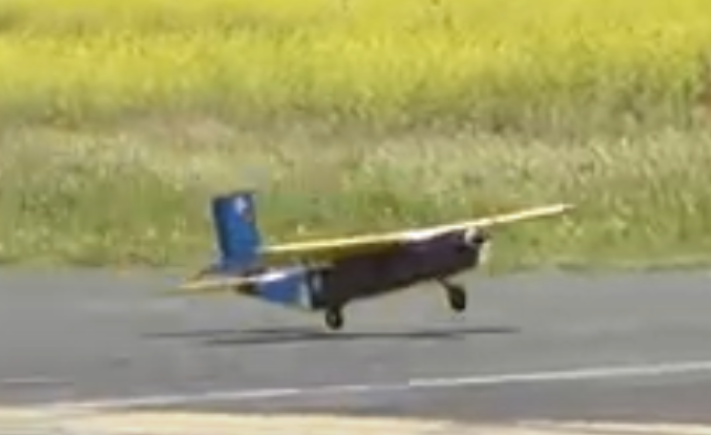
Patchwork Landing
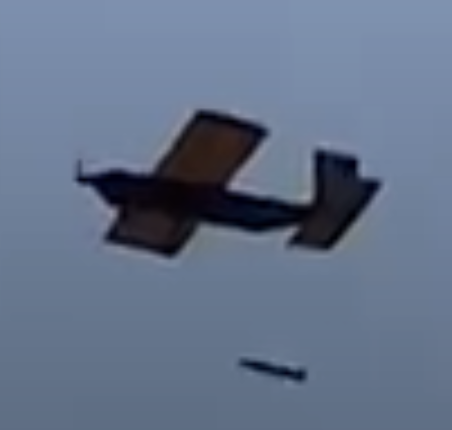
Sensor Deployed
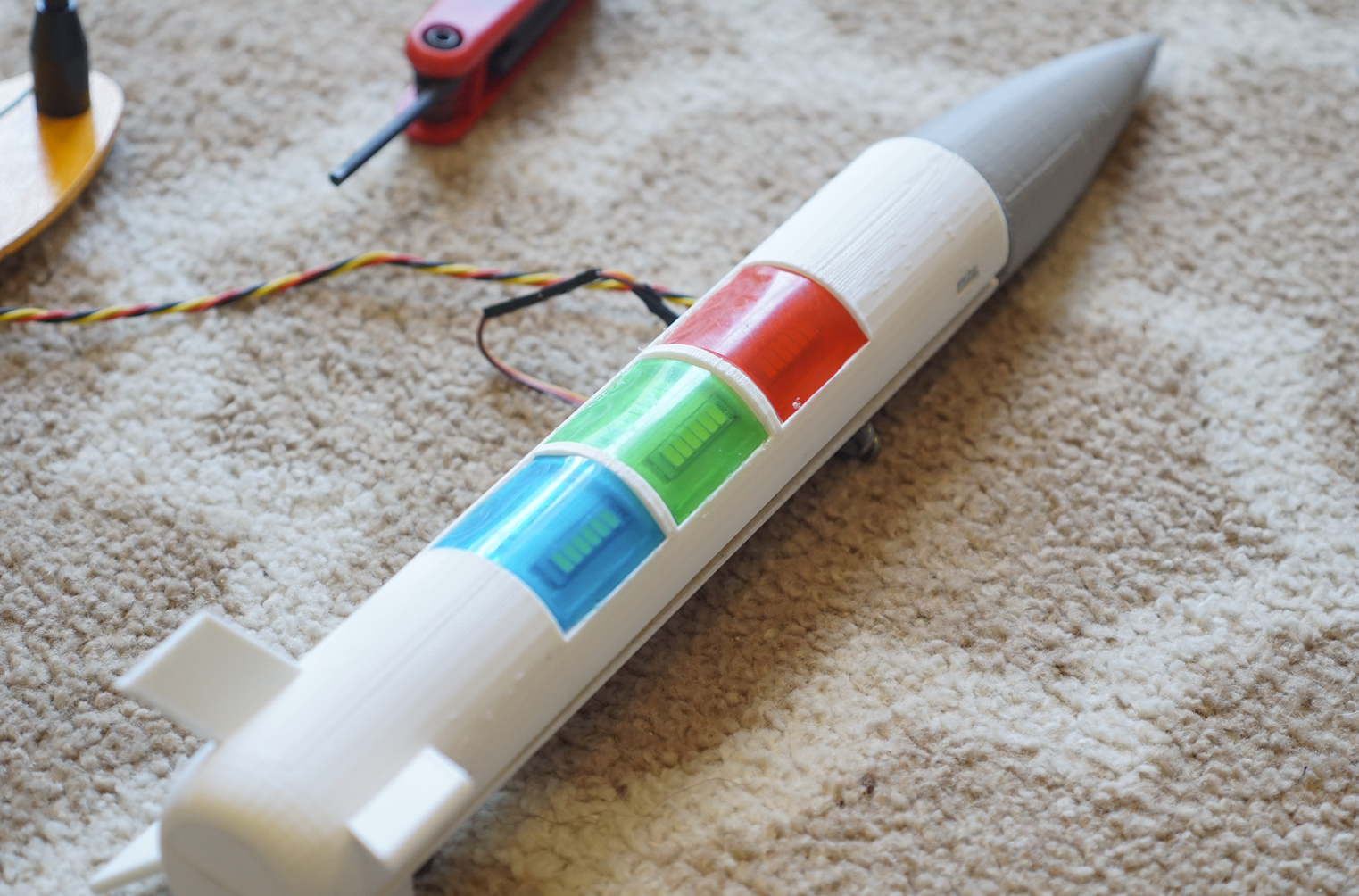
Sensor
Objectives
- Restrictions: less than 5' wingspan, less than 55 lb takeoff weight, electrically powered and propeller driven, 200 Wh battery, takeoff field of 100'.
- Flight Mission: complete 3 laps under 5 minutes.
- Shipping Mission: complete 3 laps fully loaded with sensors and containers.
- Deployment Mission: deploy and retract a cylindrical sensor in flight. The sensor shall be as long as possible and fit inside the aircraft. The sensor shall also be reasonably aerodynamic as it's being towed in-air.
- Complete all design, manufacturing, and testing remotely.
Skills
Mechanical Design: SolidWorks, design for manufacturing
Simulation: SolidWorks FlowSim, AVL
Prototyping: 3D printing, prototype testing
Programming: MATLAB
Manufacturing: laser cutting,
Machine Tools: heat tools, adhesives
Key Tasks
My tasks and contributions span across aerodynamics, CAD, and manufacturing.

NACA 2410 Cross Section
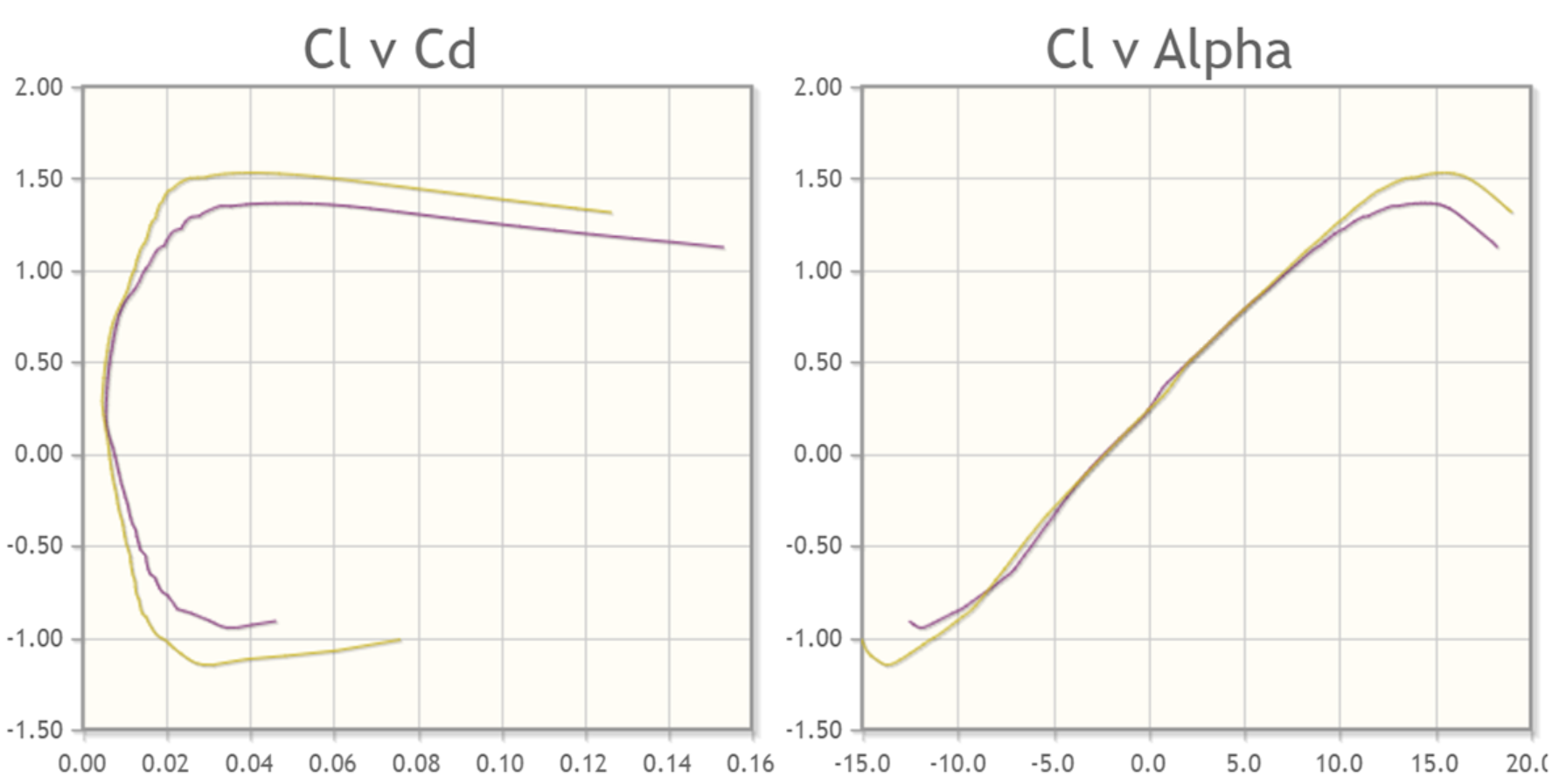
Performance Specifications for NACA 2410; Credit: airfoiltools.com
Aerodynamics
- Conducted a Figure-of-Merit (FOM) trade study to select the primary wing airfoil; picked NACA 2410.
- Studied the lift, drag, and pitch behaviors of 65 different common airfoils listed on an online database.
- Selected for low lift and drag coefficients at positive angles of attack to increase airspeed and range. Also selected for manufacturability.
- Maintained and revised a MATLAB script that calculated aerodynamic performance and estimated stability; assembled control surfaces from laser-cut balsa and heat-shrink wrap.
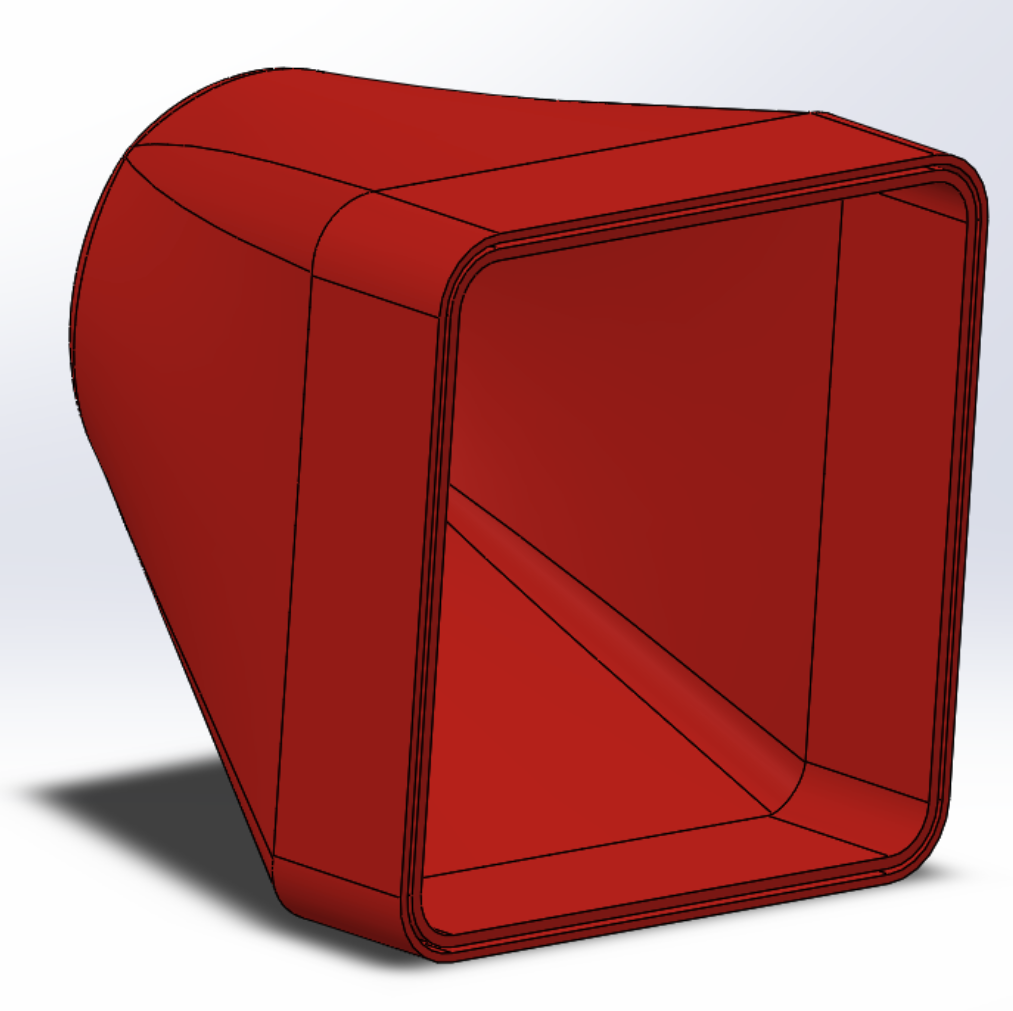
Nose Cone (black) and Nose Cone Mold (red)
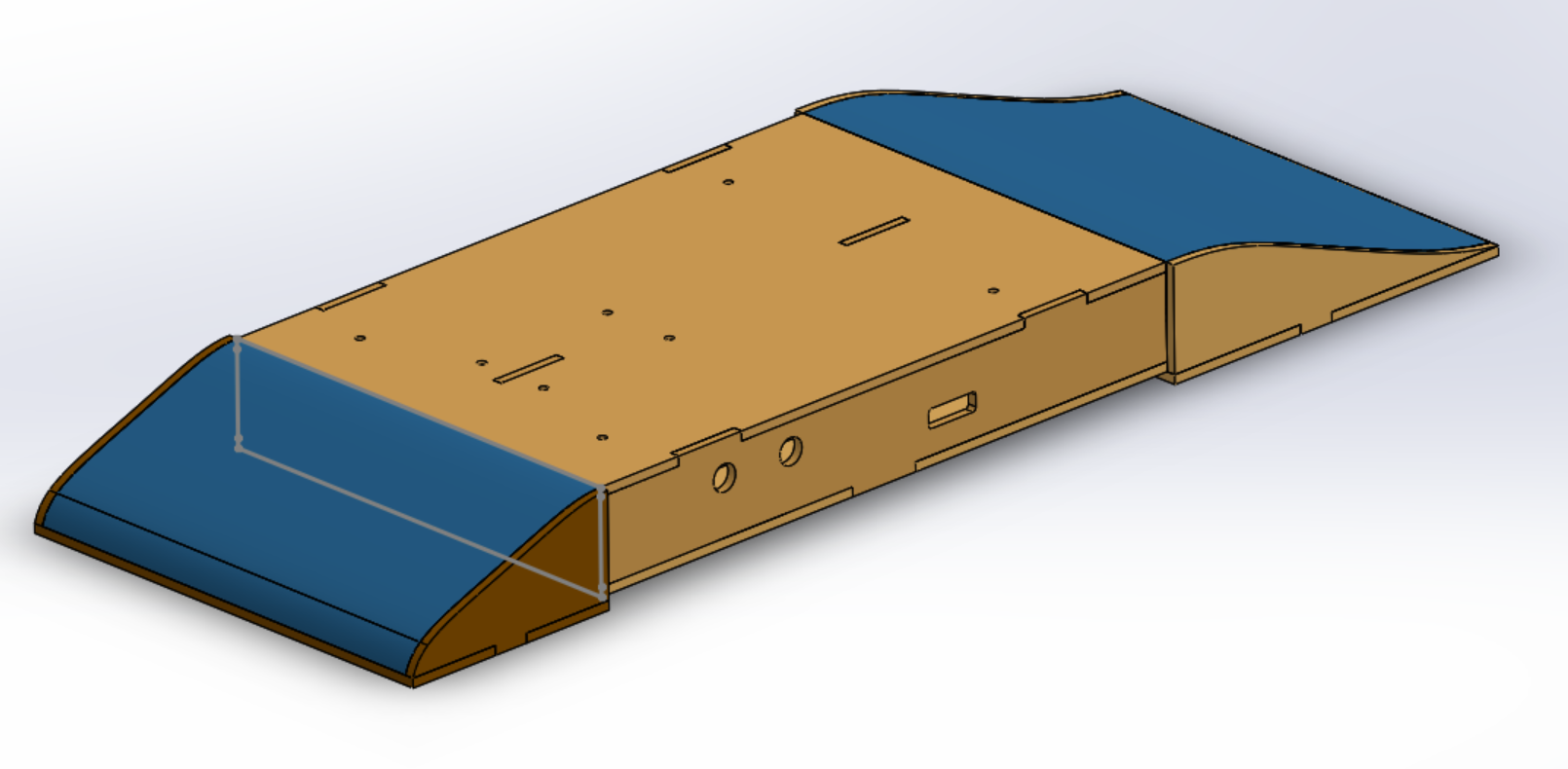
Aerodynamic Jig for the Wing Box
CAD
- Modeled the carbon fiber nose cone following the dimensions given by the Propulsions Team. Also modeled a nose cone mold, which is 3D-printed and used for the carbon fiber layup process.
- Modeled aerodynamic surface jigs for the wing box and the tail box. Jigs were assembled out of laser-cut balsa and used to create foam shapes that guides airflow over the wing and tail boxes.
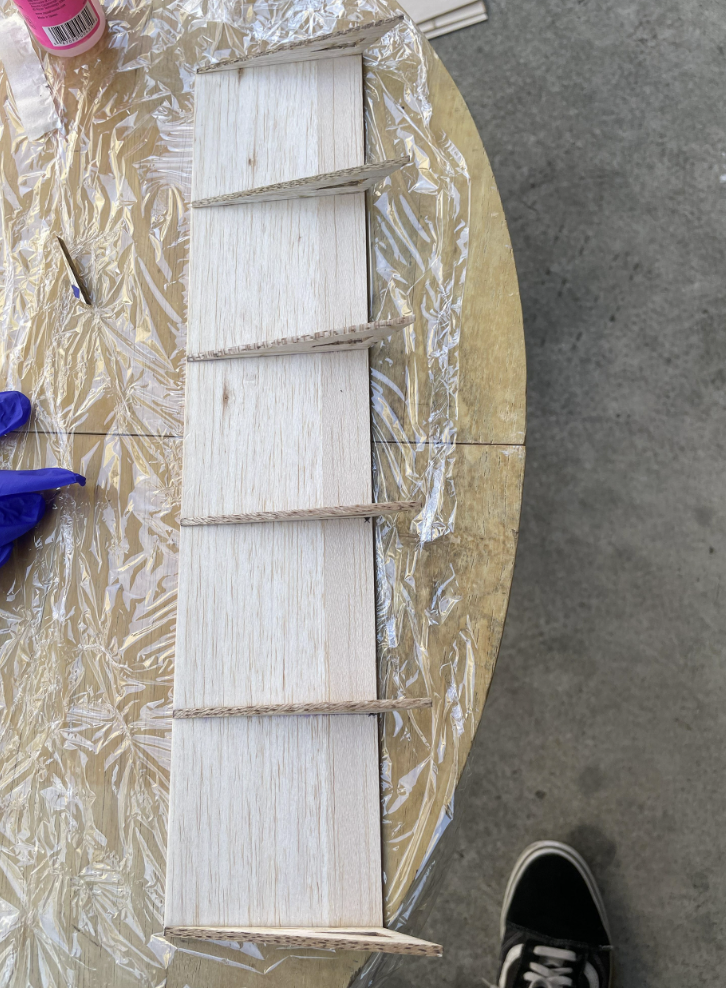
Joining Ribs for Ailerons
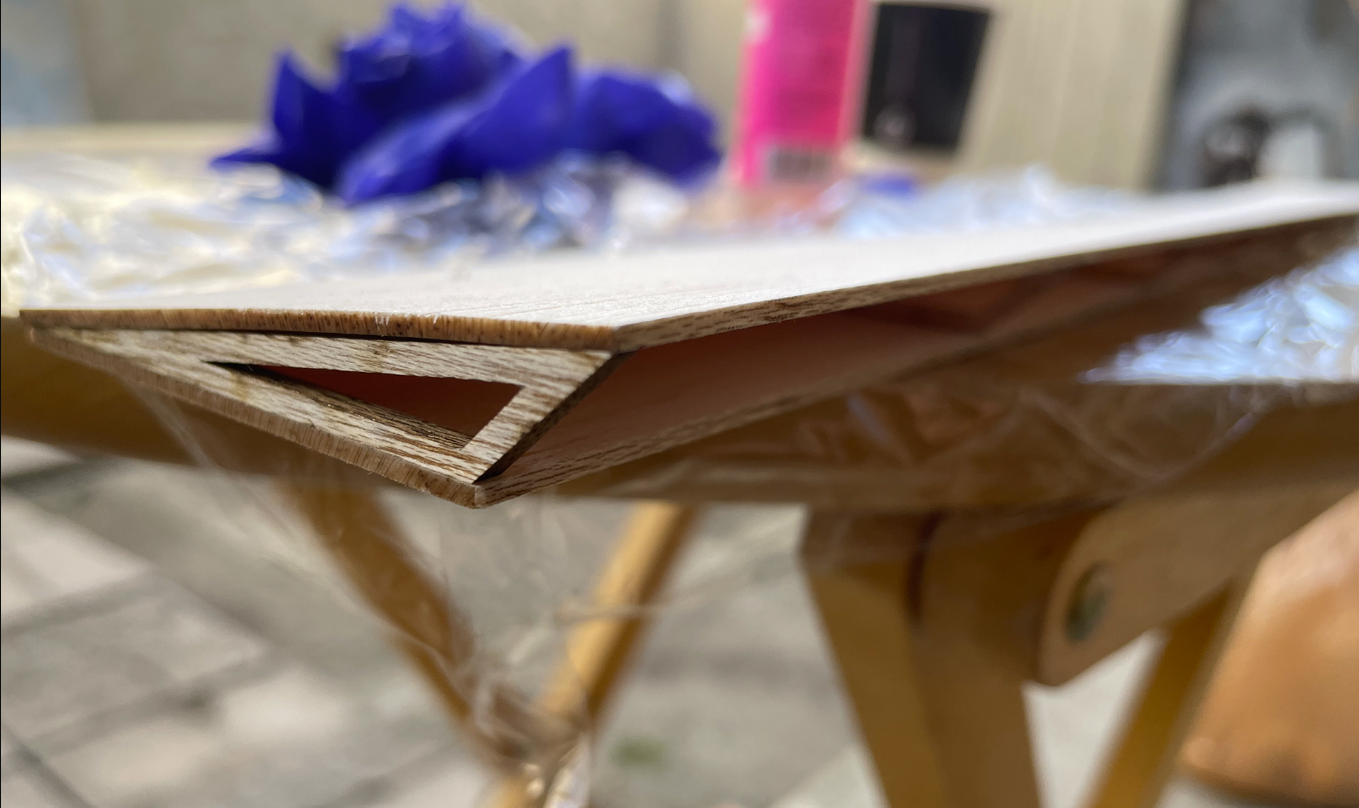
Assembled Aileron before MonoKote
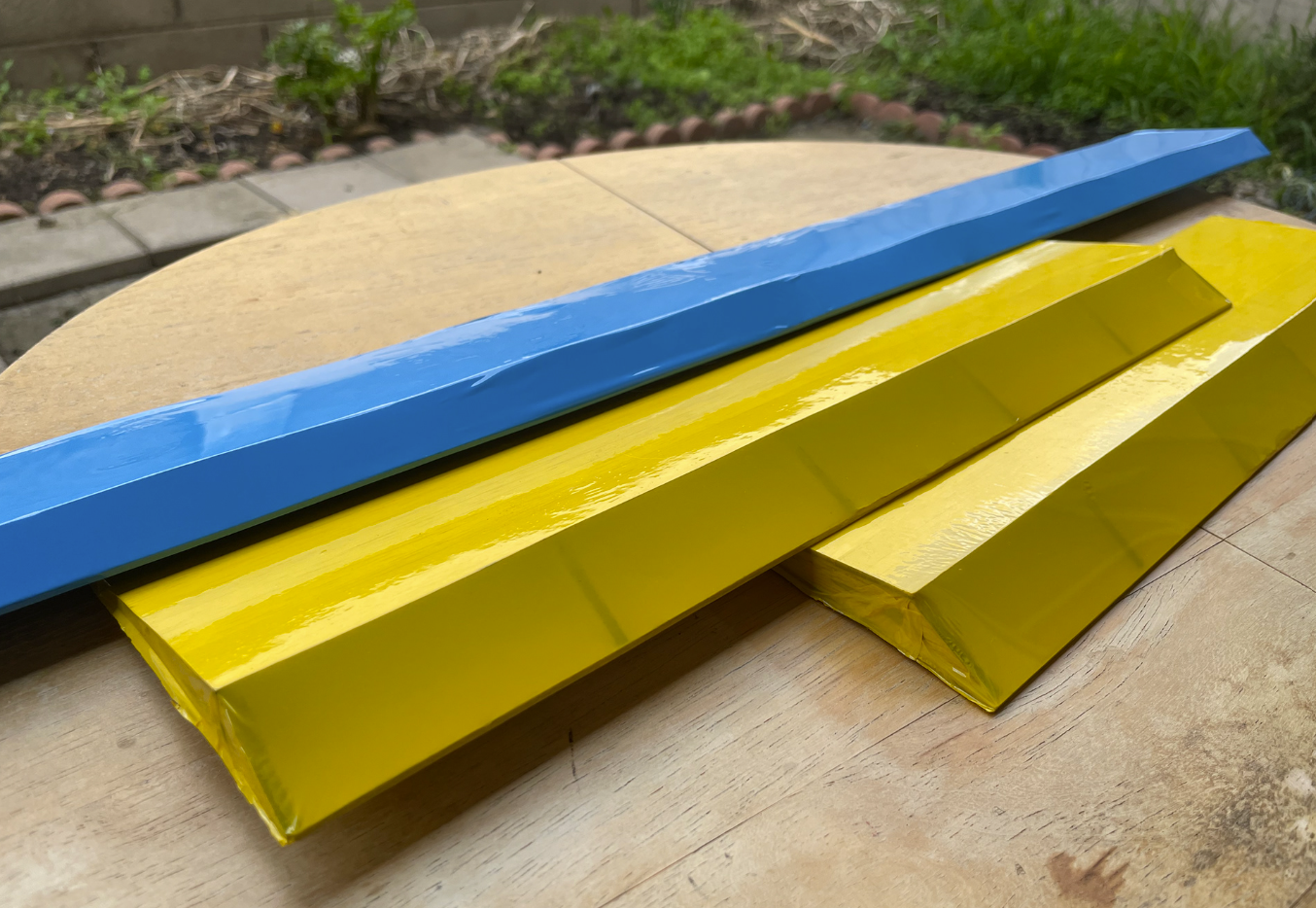
Completed Ailerons and Elevator
Manufacturing
- Assembled the aerodynamic control surfaces (ailerons, elevators, rudder). Ribs were laser-cut out of balsa pieces and joined using cyanoacrylate (CA) glue.
- Applied heat shrink plastic "MonoKote" wrap using heating iron and heat gun to increase surface smoothness and maintain aerodynamic shape. Optimized aerodynamic performance of the wings while minimally increasing weight.
Outcomes
- Our competition aircraft, Patchwork, is a high wing monoplane with a conventional tail and tricycle landing gears. It has a wingspan of 59". The single tractor motor and propeller at the tip of the nose pulls the 15lb aircraft. The fuselage, nose cone, and tail cone are made of carbon fiber, while the wing, stabilizers, and control surfaces are made out of laser-cut balsa and spruce wood.
- Designed and tested a 3D-printed rocket-shaped sensor with a 3/4" diameter, 15" length, and 4 small guide fins. The sensors are deployed, towed, and retracted in-flight using an electric motor-driven winch system and a bomb-bay door.
- We typically build two or three prototypes throughout the year, but were only able to build one due to remote work. This limited the testing of our sensor deployment mechanism.
- Won 14th / 93 (15.2%) in design report scores and 28th / 92 (30.4%) in overall competition scores.
- I joined with almost no knowledge of designing and building aircrafts. Throughout the year, I learned and applied SolidWorks, MATLAB, many manufacturing techniques, as well as aerodynamic optimization.
Links
AIAA DBF Competition: https://www.aiaa.org/dbf
DBF at UCLA Website: https://dbfatucla.github.io/DBFatUCLA/index.html
DBF at UCLA YouTube: https://www.youtube.com/channel/UCDAtxmGCshJuw95zDNmqnkg
DBF at UCLA Instagram: https://www.instagram.com/dbf_ucla/